In this ever-changing world, businesses need to keep up with these changes or be left behind. 64% of business executives believe their companies need to build new strategies around digitization to remain viable and sustain productivity through 2023, while only 11% say their current business models will be economically viable.
60% of digital transformation budgets are for building internal platforms, and most especially leveraging AI. Nowadays, AI technology is everywhere. It’s being used in mobile apps, software, hardware, automatic text generation, image and data processing, you name it. AI-based, composable applications and business platforms can help reduce time to market and enhance intelligent organizational decision-making. That’s why the number of enterprises using AI in business grew by 270% between 2015 and 2019.
Another growing trend is the use of low code for internal platforms and app building. Statista Report suggests that the global market forecast for low-code is around 65 Billion U.S. by 2027. And it is expected to reach $187 Billion by 2030. That’s a CAGR of 31.1% for 2020–2030.
In a previous blog, we’ve seen the overall benefits of digitization. Now, one may wonder: are the digitization strategies and benefits the same for all industries? The answer, of course, is no. One should consider, for starters, different regulatory environments, geographies, and customers, along with different business requirements and objectives, among others.
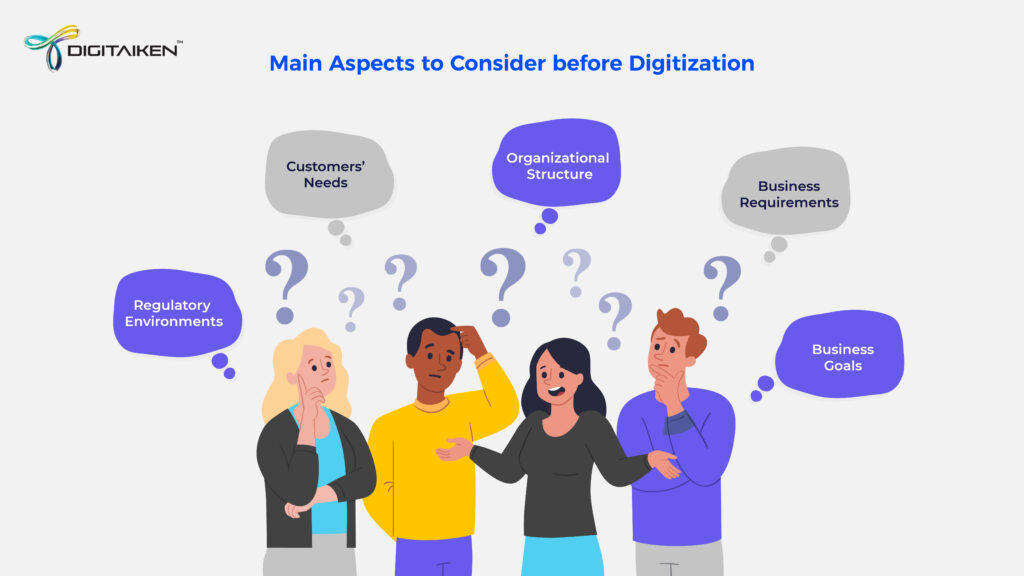
Digitization in Financial Services
The financial sector is currently facing a multitude of challenges, being social distancing requirements the most pressing for firms. The pandemic changed radically the relationship between banks and their customers, including limiting branch access and hours for in-person assistance and encouraging the usage of mobile apps and contactless payment methods, and many financial institutions were forced to become part of the digital banking ecosystem.
Banking processes need to adjust to this changing environment to serve customers better, support employees’ productivity and optimize operations. This is why digitalizing processes is beneficial for financial companies.
Top 5 benefits of a digital infrastructure for the Financial Sector include:
- Automatic storage and big data. Every single day financial organizations generate large amounts of data from hundreds of card transactions, loans, insurance documents, and payments. With traditional IT setups, constant upgrades and maintenance are required, whereas a cloud approach can provide unlimited storage and automatic backups, to ensure data availability and avoid human error.
- Enhanced security and reliability. With digital communications and banking processes, it is more important than ever to both backup data and apply appropriate policies to ensure the information sent out and received is encrypted and safely stored. A cloud-first approach ensures all data is backed up automatically while ensuring high-security standards, protecting it from all kinds of threats. At the same time, cloud systems allow all documentation and data points to be accessed from authorized websites worldwide with utmost ease.
- Robust reporting and interactive dashboards. With all key data stored in one system, business leaders can easily track KPIs in advanced CRM and process management systems. For banking institutions, it is crucial to keep track of their numbers to be sure they are compliant with all regulations. Leveraging the use of CRM and cloud data storage allows for well-designed dashboards and cross-organizational KPI lists for an accurate evaluation of the overall business performance in all transactions and services, and compliance: revenue, expenses, operating profit, operating expenses as a percentage of assets, assets under management (AUM), percentage of AUM above benchmark, return on equity, and return on assets (ROA).
- Increased business agility and mobility. A digital and cloud-first approach allows banks and credit unions to leverage Artificial Intelligence, Cloud computing, and Low-Code development to agilize their operations. Artificial intelligence can help automate manual work, detect, and prevent fraud, as well as improve customer experience. Cloud computing enables employees with appropriate access to work on the go, so they can use any device for real-time monitoring and analysis, as well as access company emails, business applications, and CRM tools when they are out of the office. On the other hand, Low-code development platforms provide the ability to build new apps and software functionality quicker, thus ensuring policy enforcement, and keeping the customer experience consistent across all channels, all while decreasing app development and maintenance costs. By adopting a powerful low-code platform, financial institutions can build future-proof software that can be easily updated to stay ahead of the competition, increase revenue, and be adaptable to the constantly changing climate in the fast-paced industry.
- Reduced maintenance costs. Digitization allows for less infrastructure for your business to maintain onsite. As a result, the cost associated with everyday maintenance is notably lowered. Moreover, with AI and Low-code development, all business processes are automated, saving time and money in the process.
Manufacturing Industry
Manufacturing companies can benefit from digital technology not only in product planning and sales but also in production and distribution, maximizing efficiency and raising productivity. The top 5 benefits of digitization for manufacturing companies are:
- Enhanced factory production performance and traceability. Incorporating smart technology such as AI, robotics, IoT, automation systems, and other digital tools can optimize the overall manufacturing process. For example, sensors can be used to monitor the condition of the casks and alert warehouse managers when temperature or humidity thresholds are about to be compromised, allowing warehousing staff to take corrective action and ensuring service quality and greater customer confidence. Benefits include reducing human errors or injuries, relieving workers from complex tasks and monotonous schedules, increasing production rates, improving quality and compliance, and more. Moreover, by digitizing paper documents, smart warehouses can make document storage centres more efficient and reliable. Warehouses with automated storage and retrieval systems (AS/RS) use the available space more efficiently, reducing the number of trained employees required and keeping the workers in the warehouse safe since they won’t need to operate forklifts or other heavy machinery for item storage.
- Accelerated decision-making. Digital transformation in manufacturing industries has revolutionized operation management. Monitoring real-time data improves the ability of supervisors to make informed and accurate decisions to improve quality, performance, and productivity. It also offers companies a better picture of the market by providing better insights into customer behaviour and purchasing power to rapidly respond to changing consumer needs. Also, it helps in getting accurate and real-time information about the cost and time involved in various processes.
- Optimized costs and reduced waste. Migrating the supply chain management systems, product information systems, and information management tools used by sales reps to a cloud-first approach can optimize production costs, and reduce WIP and inventory. Modern IoT and analytics systems can be linked with core business systems for automatic data retrieval and stock and material flow monitoring. This provides real-time analysis of the warehouse’s current production and helps identify weak points. Leveraging this innovative methodology of processes can reduce operating expenditures and avoid wasting time in non-value-adding or time-consuming processes, thus reducing waste, streamlining workflows, improving processes and stable operations.
- Improved communication. Digitization promotes a better flow of data communication between employees and departments, encouraging open communication and collaboration. The automated communication model provides accessibility irrespective of time or place, increasing efficiency, accuracy, and responsiveness, as employees can connect and use any device from anywhere without having to keep apps and data on client devices. It’s also a reliable solution from a security perspective. Moreover, it allows for enhanced communications with suppliers. Through real-time communications, you can find out where your supplies are at any given time, thus improving supply chain information and better operations management.
- Sales, distribution, and shelf-tracking. Improving production is of no use if the products don’t reach retail. AI-enabled sales and distribution systems alongside IoT technologies make it easier to manage master data, configure systems, process payments, process sales orders, deliveries, prices, invoices, etc. and can help track product distribution and shelf availability. Learn in our case study how our AI-based shelf intelligence solution helped a global supply chain leader increase operational efficiency, and save time, among other benefits, with real-time monitoring of shelves.
Automotive Industry
Similarly to the manufacturing industry, digitization in the automotive industry can deliver advantages both in production lines and distribution, accelerating efficiency and improving user experience, key factors in increasing ROI. These are the top 5 benefits of digitization in the Automotive Industry:
- Enhanced efficiency in production lines. Internet of Things (IoT) solutions help innovate supply chains. In vehicle production, brands must apply different labels with country-specific safety, usability, and specification data. Any damaged, incorrect, or missing labels could pose regulatory issues. Instead of depending on manual inspections, labels can be inspected automatically on the plant floor with IoT-enabled devices, avoiding human error in the process, as employees are not always able to read the labels to confirm accuracy. In the assembly line, sensor-equipped technology can provide greater accuracy and quality in the stamping process. Sensors can automatically adjust the amount of material needed for each part of the vehicle by measuring the force exerted on the blanks and adjusting the pressure by lowering or raising stamping dies, avoiding components tearing apart or stability being affected by either too much or too little material used. This can help reduce machine downtime by 20-35% and overall plant maintenance costs by 15-25%. Also, automated cameras can be used to photograph labels and parts and send them to the cloud for analysis. An AI-based system analyses the data, and if an anomaly is detected, it can notify an in-line worker for the issue to be checked. This results in actionable insights to fix detected errors.
- Improved quality of the finished vehicle. Automotive companies follow stringent quality control processes to ensure each vehicle meets regulatory standards. Leveraging machine learning, the digital production platform can connect data from all machines, plants, and systems at all factory sites to increase plant efficiency and uptime and enhance production flexibility. As issues are detected and corrected on the assembly line itself, vehicle quality is greatly improved.
- Advanced modelling and simulation techniques. To meet accelerated engineering schedules and reduce the need for physical prototypes, many vehicle manufacturers rely on advanced modelling and simulation techniques that allow engineers to test new concepts and designs. This is not possible without AI and high computing capacity. With computer-aided engineering simulations, engineers can bring their designs to market quickly, extend vehicles’ range, and maintain high safety standards.
- Access resources on demand. Migrating production environments to the cloud allows engineers to access and automate resources on demand, delivering cost-effective high performance at a low price-per-compute ratio. Backup synchronization can be automated, improving overall time expenditure and avoiding loss by human error. This also enables collaboration through shared storage.
- Improving end-user experience: Relying solely on manual guides it’s in the past. These guides state the same instructions and guidelines for everyone, but not all these instructions are appropriate for every vehicle. AI-powered sensors in vehicles can drive the owner’s attention toward the specific system parts that need service. AI also allows for predictive maintenance that informs the driver about any possible issues before they happen, thus avoiding the risk of breakdowns or major accidents.
At DigiTaiken, we’ve come to understand that the business goals of several sectors can be better achieved through digitization and thus yield a high ROI. With the right professionals and skills, we have built and delivered digital solutions customized to the specific needs of each industry, producing exceptional business value and driving successful transformations to the finish line.